Blog
-
Divest Impex
Cargo Pants Prototypes: 13 Proven Ways to Speed Up Development
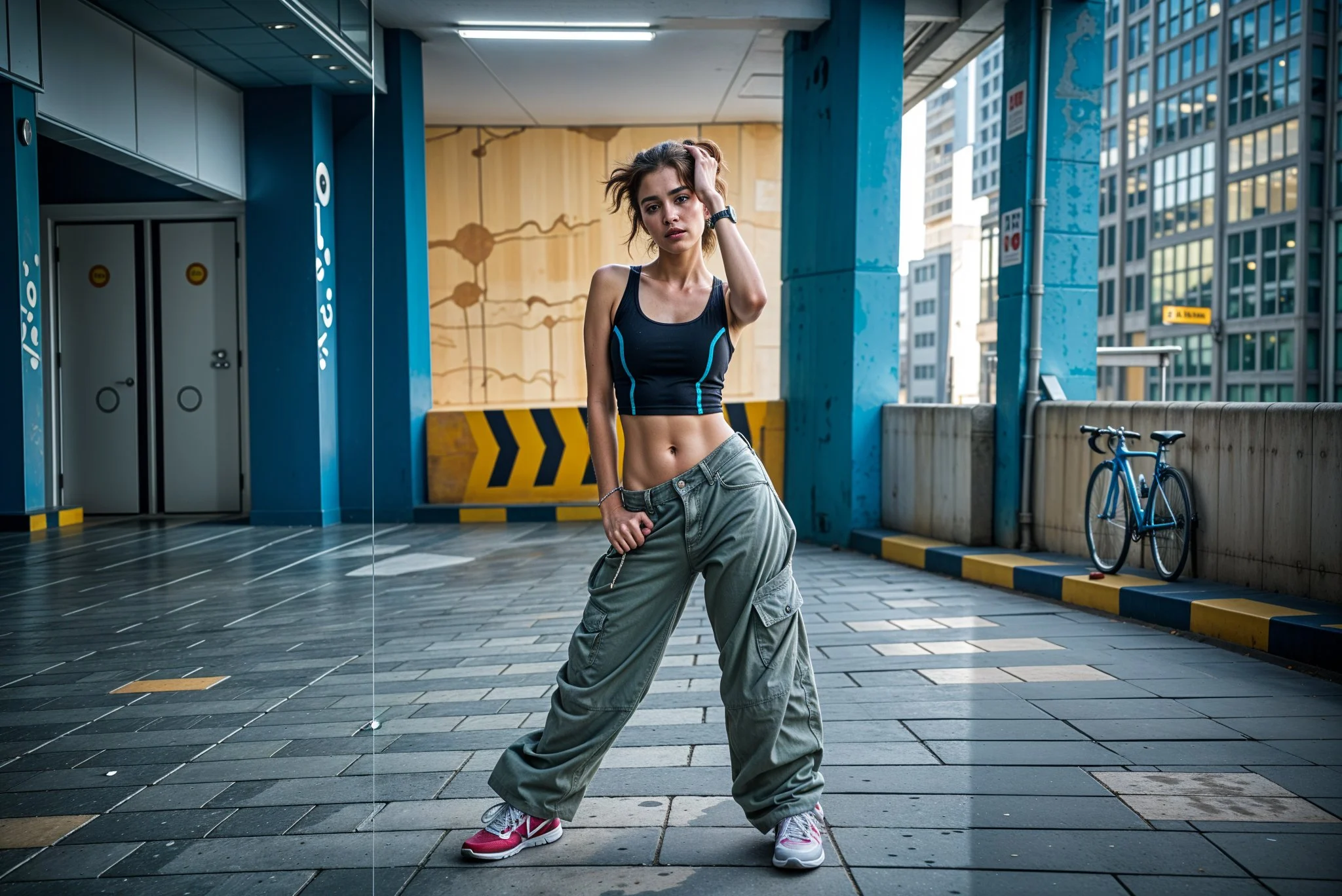
Mins To Read
Table of Contents
ToggleIn the fast-paced world of fashion and apparel, getting your designs to market quickly can be the difference between a trendsetter and a forgotten idea. For brands developing new collections, particularly those featuring functional and stylish items like cargo pants, the efficiency of creating **cargo pants prototypes** is paramount. Streamlining this development phase not only saves time and resources but also allows designers to iterate faster, perfect their vision, and respond to consumer demand with agility. This guide delves into proven strategies and expert insights to significantly reduce your apparel prototype lead time.
Developing high-quality cargo pants involves a meticulous process, from initial sketch to final production. However, it’s the prototyping stage where ideas truly come to life, and where bottlenecks often occur. By focusing on smart planning, leveraging modern tools, and adopting a collaborative approach, businesses can accelerate their prototype development without compromising on quality or design integrity. Let’s explore how to achieve this.
—
Why Rapid Prototyping is Key for Cargo Pants
The journey from a design concept to a tangible product is fraught with potential delays. For **cargo pants prototypes**, this journey often involves intricate pocket designs, durable fabric choices, and specific fit considerations. Rapid prototyping isn’t just about speed; it’s about agility, cost-effectiveness, and responsiveness. In a competitive market, being able to quickly test, refine, and approve designs gives you a significant edge.
Faster prototyping means you can present samples to buyers sooner, test market viability, and make necessary adjustments before committing to large-scale production. This reduces the risk of costly errors and ensures that the final product truly resonates with your target audience. For a brand like Divest Impex, known for its commitment to quality and efficient production, understanding the nuances of quick cargo pants sampling is fundamental to delivering exceptional apparel.
Moreover, rapid development cycles allow for more iterations. Each prototype serves as a learning opportunity, refining the fit, functionality, and aesthetic of the cargo pants. This iterative process is crucial for achieving perfection and meeting the high standards consumers expect from modern apparel.
—
Understanding Your Design Goals Before Prototyping
Before a single stitch is made, a clear understanding of your design goals is essential for efficient **cargo pants prototypes**. What is the purpose of these cargo pants? Are they for outdoor adventure, everyday casual wear, or a more fashion-forward statement? Defining the target audience, their needs, and the intended use will guide every decision from fabric selection to pocket placement.
Start by outlining specific details:
- Target Demographic: Who will wear these cargo pants (e.g., men, women, kids, specific age groups)? Divest Impex offers a range of options, from custom men’s cargo pants to custom women’s cargo pants and even custom kids’ cargo pants, highlighting the importance of tailored designs.
- Functionality: How many pockets are needed? What closures? Are knee reinforcements or adjustable hems required?
- Aesthetics: What is the desired silhouette (slim, relaxed, baggy)? What is the overall style and color palette?
- Cost Targets: Establish a realistic budget for materials and production to inform design choices.
A well-defined design brief acts as a blueprint, minimizing ambiguity and reducing the need for extensive revisions later in the development cycle. This upfront planning is a cornerstone of fast cargo pants prototype development.
—
Choosing the Right Fabrics and Materials for Your Prototypes
The selection of fabrics and materials is a critical step that directly impacts the look, feel, and functionality of your **cargo pants prototypes**. Choosing the wrong material can lead to fit issues, performance problems, and necessitate costly re-prototyping. For initial prototypes, you might consider using a material that mimics the drape and weight of your final fabric but is less expensive, especially if the final fabric is very costly or difficult to acquire quickly.
Material Considerations for Cargo Pants
- Durability: Cargo pants are often designed for rugged use, so durable fabrics like cotton twill, ripstop, canvas, or blends are common.
- Weight and Hand: The weight of the fabric influences drape and comfort. The “hand” refers to how the fabric feels to the touch – soft, crisp, stiff.
- Stretch: Incorporating a small percentage of elastane or spandex can enhance comfort and movement.
- Colorfastness and Shrinkage: Consider how the fabric will react to washing and wear.
- Availability: Can you source the chosen fabric quickly and consistently for both prototyping and production?
For pocketing, consider materials that are strong enough to hold items without tearing, yet flexible enough not to add bulk. Zippers, buttons, and other notions should also be selected with quality and functionality in mind. Making informed material choices early on is vital for reducing apparel prototype lead time.
—
Leveraging Digital Tools for Faster Design (CAD & 3D Modeling)
The advent of digital tools has revolutionized the apparel design and prototyping process. Computer-Aided Design (CAD) software and 3D modeling platforms allow designers to visualize, manipulate, and even “fit” garments virtually before any physical material is cut. This significantly speeds up the initial design phases for **cargo pants prototypes**.
Benefits of Digital Prototyping:
- Virtual Sampling: Create realistic 3D renderings of your cargo pants, complete with accurate fabric drapes, textures, and prints.
- Pattern Creation: Generate precise 2D patterns directly from 3D models, minimizing manual errors.
- Fit Simulation: “Dress” virtual avatars of various body shapes and sizes to test fit and proportion, identifying potential issues early.
- Faster Iterations: Make design changes on the fly and see immediate visual feedback, reducing the need for multiple physical samples.
- Reduced Material Waste: Fewer physical samples mean less fabric waste and lower material costs.
- Improved Communication: Share 3D models with manufacturers and stakeholders for clearer communication and understanding of the design intent.
Software like CLO3D, Optitex, and Browzwear are powerful tools that can transform your workflow, making the development of custom cargo pants proto approval much more efficient. While there’s a learning curve, the long-term benefits in terms of time and cost savings are immense.
—
Creating Your First Pattern: Traditional vs. Digital Methods
The pattern is the blueprint for your **cargo pants prototypes**. Whether you opt for traditional manual pattern making or embrace digital methods, accuracy is paramount. Each method has its advantages in terms of speed and flexibility.
Traditional Pattern Making:
This involves drafting patterns manually on paper using measurements, rulers, and curves. It’s a foundational skill for many designers and offers a tactile understanding of garment construction. However, making revisions can be time-consuming, requiring re-drafting sections of the pattern.
- Pros: Hands-on, builds fundamental understanding.
- Cons: Slower for revisions, prone to human error, requires physical space.
Digital Pattern Making:
Using CAD software, patterns are created and manipulated digitally. This allows for precise adjustments, grading to different sizes, and direct integration with cutting machines. Many 3D design programs can automatically generate 2D patterns from a 3D model, streamlining the process even further.
- Pros: Faster revisions, accurate grading, direct integration with manufacturing, less material waste.
- Cons: Requires specialized software and training, initial setup cost.
For speeding up development, digital pattern making is generally superior. It enables quick adjustments based on feedback from initial **cargo pants prototypes** and prepares your designs for efficient mass production.
—
The Importance of a Muslin or Toile for Initial Fit Checks
Before cutting into your final, often more expensive, fabric for **cargo pants prototypes**, creating a muslin (or toile in French) is a crucial step. A muslin is a test garment made from an inexpensive, plain fabric (often unbleached cotton) that mimics the drape and weight of your intended material. Its primary purpose is to assess fit, proportion, and construction details without wasting valuable resources.
Why a Muslin is Indispensable:
- Early Fit Assessment: Identify and correct fit issues like waistband gapping, crotch depth, leg width, and pocket placement early in the process.
- Design Visualization: See how your 2D pattern translates into a 3D garment and evaluate the overall silhouette.
- Construction Practice: Test the sequence of construction, especially for complex features like cargo pockets, pleats, or unique closures.
- Fabric Behavior: Understand how the chosen design elements interact with a fabric similar to your final material.
- Cost Savings: Avoid cutting and potentially ruining expensive main fabric due to design or fit errors.
Even with advanced 3D modeling, a physical muslin provides invaluable tactile feedback that digital simulations cannot fully replicate. It’s a small investment of time that prevents larger, more costly setbacks, helping to ensure fast cargo pants prototype development.
—
Streamlining the Sewing Process for Prototype Efficiency
Once your pattern is finalized and materials are chosen, the sewing process for your **cargo pants prototypes** needs to be efficient. This is where skilled sample makers and a well-organized workspace come into play. Every minute saved in this stage contributes to reducing apparel prototype lead time.
Tips for Efficient Prototype Sewing:
- Clear Instructions: Provide sample makers with comprehensive pattern pieces, clear assembly instructions, and a visual reference (sketch or digital rendering).
- Organized Materials: Ensure all necessary fabrics, notions (zippers, buttons, drawstrings), and trims are readily available and prepped.
- Specialized Equipment: Use appropriate sewing machines and attachments for different fabric weights and construction details (e.g., specific presser feet for topstitching, buttonhole machines).
- Batching Operations: For multiple prototypes or complex designs, consider sewing similar components in batches (e.g., all pocket bags, then all waistbands) to build momentum.
- Quality Control at Each Step: Rather than waiting until the end, check for accuracy and quality after each major step (e.g., after attaching pockets, after joining leg seams).
- Skilled Sample Makers: Work with experienced sewers who understand the nuances of apparel construction and can troubleshoot issues on the fly. Divest Impex prides itself on its skilled team who excel in creating precise and efficient samples.
By optimizing the sewing workflow, you can significantly cut down the time it takes to produce physical **cargo pants prototypes**.
—
Conducting Effective Fit Tests and Gathering Feedback
Once a physical **cargo pants prototype** is assembled, thorough fit testing and comprehensive feedback are crucial for refinement. This stage is about identifying what works, what doesn’t, and what needs adjustment to achieve the perfect garment. An effective fit test ensures that the design truly meets the wearer’s needs and aesthetic expectations.
Key Aspects of Effective Fit Testing:
- Use the Target User: Whenever possible, fit the prototype on someone who represents your target demographic in terms of body shape and size.
- Movement and Comfort: Don’t just check static fit. Have the wearer move, sit, squat, and perform activities relevant to the cargo pants’ intended use. Do pockets snag? Is the waist comfortable? Is the range of motion restricted?
- Visual Assessment: Observe the garment from all angles. Are seams straight? Is the drape correct? Are there any unsightly pulls, wrinkles, or excess fabric?
- Detailed Feedback Form: Provide a structured way to collect feedback. Ask specific questions about comfort, fit in different areas (waist, hips, thighs, knees, inseam), pocket functionality, and overall appearance.
- Photography and Notes: Document the fit test with photos from various angles, clearly marking areas that need adjustment directly on the prototype or on the images.
- Multiple Perspectives: If possible, involve multiple individuals in the feedback process (designer, pattern maker, merchandiser) to get diverse insights.
This systematic approach to feedback helps pinpoint precise areas for improvement, making the subsequent iteration phase much more targeted and efficient for custom cargo pants proto approval.
—
Iterating Quickly: Making Adjustments to Your Prototype
The feedback gathered from fit tests is the fuel for iteration. This is where your **cargo pants prototypes** truly evolve. The goal is to make necessary adjustments to the pattern or construction quickly and efficiently, minimizing delays in the development cycle.
Strategies for Rapid Iteration:
- Prioritize Feedback: Focus on critical issues first (e.g., major fit problems) before addressing minor aesthetic tweaks.
- Precise Pattern Adjustments: Translate feedback directly into accurate pattern modifications. Digital pattern making excels here, allowing for swift changes.
- Targeted Re-prototyping: If a minor adjustment is needed (e.g., changing a pocket size), sometimes only a specific part of the garment needs to be re-prototyped, not the entire piece.
- Maintain Communication: Keep all stakeholders (designers, pattern makers, sample room, manufacturers) informed of changes. Effective communication for samples is vital.
- Version Control: Keep meticulous records of each prototype version and the changes made. This prevents confusion and ensures you’re always working on the latest, most refined version.
- Lean Approach: Embrace a “fail fast” mentality. It’s better to discover and fix issues early in the prototyping stage than after mass production begins.
Each iteration should bring you closer to the final approved sample, reflecting the collaborative efforts and commitment to quality inherent in Divest Impex’s development process.
—
The Role of Tech Packs in Prototype Development
A well-structured **tech pack** is arguably the most crucial document for efficient **cargo pants prototypes** and subsequent production. It serves as the comprehensive blueprint that communicates every detail of your design to manufacturers, pattern makers, and sample rooms. A detailed tech pack minimizes assumptions and reduces the need for constant back-and-forth communication, significantly speeding up the process.
What a Comprehensive Tech Pack Includes:
- Design Specifications: Front and back sketches, detailed call-outs for design features (pockets, closures, stitching).
- Bill of Materials (BOM): A complete list of all fabrics, trims, and notions, including their suppliers, colors, and quantities.
- Measurement Specs: Detailed measurements for all sizes, typically presented in a chart format. This includes crucial measurements for cargo pants like waistband circumference, inseam, thigh width, and pocket dimensions.
- Construction Details: Specific instructions on how the garment should be sewn, including stitch types, seam allowances, and finishing techniques.
- Artwork and Print Placement: If applicable, details on logos, graphics, and their precise placement.
- Colorways: Information for all color options.
- Grading Rules: How the measurements will increase or decrease across different sizes.
Investing time in creating a thorough tech pack upfront pays dividends by ensuring that everyone involved in the prototyping process has a clear and consistent understanding of your vision. This is particularly important for fast cargo pants prototype development and when working with offshore manufacturers.
—
When to Consider Outsourcing Prototype Creation
While some brands handle all prototyping in-house, there are compelling reasons to consider outsourcing the creation of your **cargo pants prototypes**. This decision often comes down to internal capabilities, budget, and the need for specialized expertise or faster turnaround times.
Benefits of Outsourcing Prototypes:
- Specialized Expertise: Prototype development factories or studios often have highly skilled pattern makers and sample sewers who specialize in specific garment types, like complex cargo pants.
- Faster Turnaround: Dedicated prototype facilities are set up for efficiency, potentially offering quicker lead times than an overloaded in-house team.
- Access to Technology: Outsourcing can provide access to advanced machinery and digital tools without the need for significant capital investment.
- Cost Efficiency (in some cases): While there’s an upfront cost, avoiding the overhead of maintaining an in-house sample room (staff, equipment, materials) can be more cost-effective for smaller brands or those with fluctuating prototyping needs.
- Focus on Core Competencies: Allows your internal team to focus on design, marketing, and sales while specialists handle the technical aspects of prototyping.
- Reduced Bottlenecks: If your in-house team is swamped with production, outsourcing can prevent prototyping from becoming a bottleneck.
When considering outsourcing, thoroughly vet potential partners for their experience with cargo pants, communication practices (crucial for effective communication for samples), and ability to meet your specific requirements. Divest Impex, for instance, works with a network of trusted partners to ensure efficient and high-quality prototype development.
—
Best Practices for Documenting Your Prototype Journey
Thorough documentation is often overlooked but is absolutely vital for speeding up development and ensuring a smooth transition from **cargo pants prototypes** to production. It serves as a historical record, a reference point for future designs, and a crucial tool for troubleshooting.
Essential Documentation Practices:
- Version Control: Label each prototype clearly (e.g., Proto 1, Proto 2, SMS sample) with dates and specific changes made.
- Fit Comments & Photos: Keep a detailed log of all fit comments, along with annotated photos showing areas of concern and proposed solutions.
- Measurement Charts: Maintain updated measurement charts for each prototype version, reflecting any adjustments made.
- Material Swatches: Attach swatches of all fabrics, trims, and notions used in each prototype to the corresponding documentation.
- Construction Notes: Document any special sewing techniques or construction methods developed during prototyping.
- Communication Log: Keep a record of all significant communications related to the prototype, especially between designers and manufacturers.
- Digital Archive: Store all digital files (patterns, tech packs, 3D renderings) in an organized and easily accessible manner.
This meticulous record-keeping reduces the chances of errors, clarifies previous decisions, and ensures that the final approved **cargo pants prototype** is perfectly replicated in bulk production. It’s a cornerstone of effective communication for samples and long-term success.
—
Frequently Asked Questions About Cargo Pants Prototyping
Q1: How long does it typically take to develop a cargo pants prototype?
A1: The timeline for **cargo pants prototypes** can vary widely based on complexity, material availability, and the efficiency of the development process. With highly organized planning and leveraging digital tools, initial prototypes can sometimes be developed in a matter of weeks. However, a complete cycle including multiple iterations for custom cargo pants proto approval can take anywhere from 4-8 weeks, or even longer for highly intricate designs. Implementing strategies like those employed by Divest Impex, focusing on clear communication and efficient processes, can significantly reduce this.
Q2: What’s the biggest challenge in speeding up cargo pants prototype development?
A2: One of the biggest challenges is often communication breakdowns between designers, pattern makers, and manufacturers. Ambiguous instructions or delayed feedback can cause significant hold-ups. Another challenge is sourcing specific or unique materials, which can extend the lead time. Overcoming these requires clear tech packs, responsive teams, and strong supplier relationships, as detailed in resources like this article on getting your tech pack right.
Q3: Can 3D modeling completely replace physical cargo pants prototypes?
A3: While 3D modeling significantly reduces the number of physical samples needed and speeds up early design visualization, it generally cannot completely replace all physical **cargo pants prototypes**. A physical sample is still crucial for assessing true drape, hand-feel of the fabric, subtle fit nuances, and real-world functionality that digital models might not fully capture. However, it drastically reduces the number of physical iterations required.
Q4: What’s a “fit sample” versus a “salesman sample” for cargo pants?
A4: A **fit sample** (often the first or second physical prototype) is created specifically to assess the garment’s fit, comfort, and general silhouette. It’s typically made in a standard size and used for internal adjustments. A **salesman sample** (SMS sample) is a near-final version of the garment, often made in the correct fabric, color, and with all trims, designed to be shown to buyers and used for marketing purposes. It’s usually produced after the fit and design have been approved through prior **cargo pants prototypes**.
Q5: How can a brand ensure effective communication for samples with an overseas manufacturer?
A5: Effective communication for samples with overseas manufacturers is crucial. This involves providing extremely detailed tech packs with clear sketches and precise measurements, using visual aids like annotated photos and videos, scheduling regular video calls to discuss progress, and having a dedicated point of contact. Using consistent terminology and confirming understanding at each step also helps prevent misunderstandings and ensures fast cargo pants prototype development. Further insights into global sourcing and communication can be found on business resources like Forbes.
Newsletter
Subscribe my newsletter to get the latest posts delivered right to your email.