Blog
-
Divest Impex
Avoiding Sweatshirt Shrinkage: Proven Tips for Manufacturers
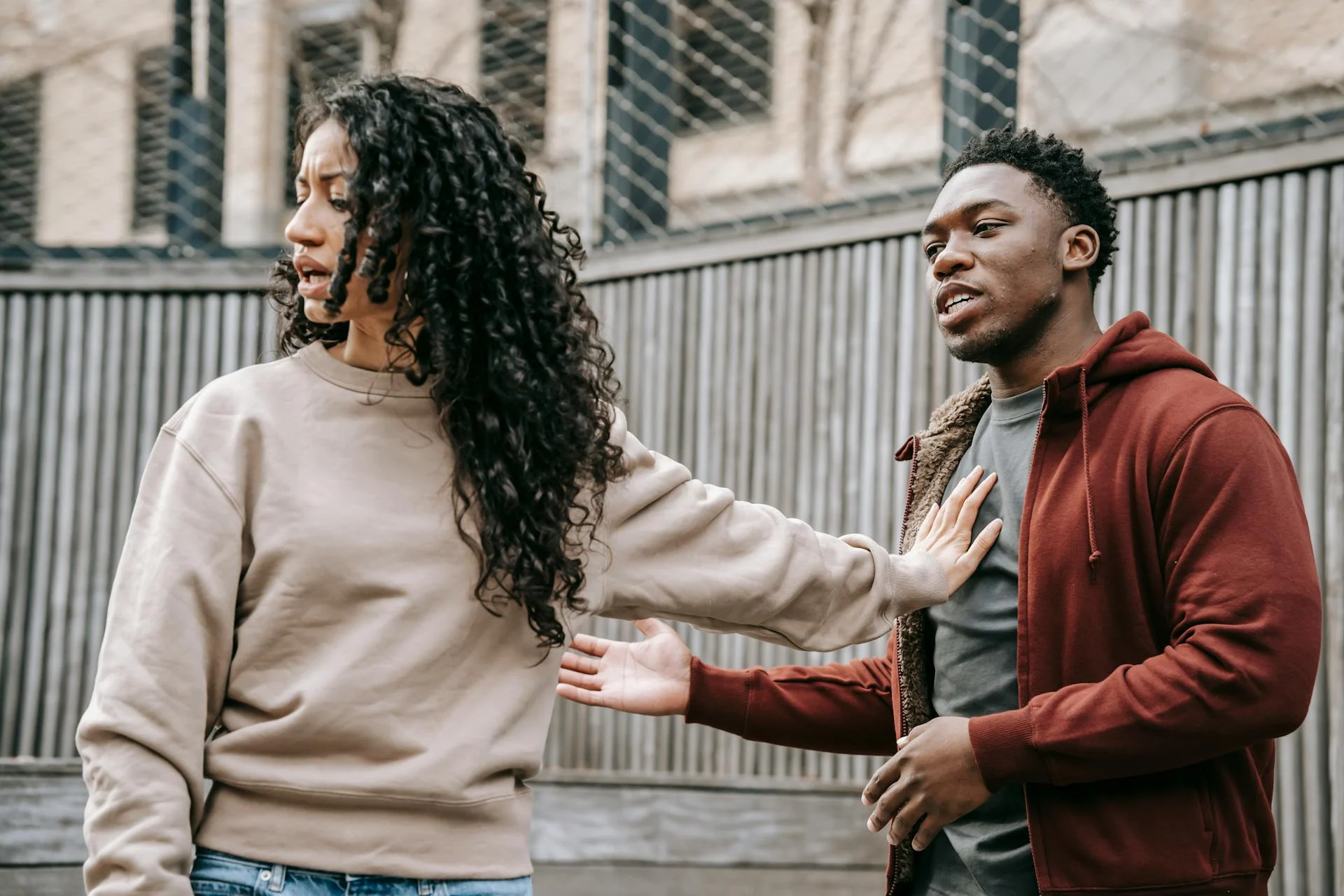
Mins To Read
Table of Contents
ToggleFor any apparel manufacturer, delivering a high-quality product is paramount to building a strong brand reputation and ensuring customer satisfaction. Among the most common and frustrating issues faced by consumers is garment shrinkage, particularly with cozy and comfortable items like sweatshirts. Mastering the art of **avoiding sweatshirt shrinkage** is a key differentiator in the competitive custom apparel industry. It’s a technical challenge that, when solved, establishes your brand as a leader in quality and reliability.
This comprehensive guide is designed for manufacturers who want to take control of their production process and guarantee consistent sizing. We will delve into the science behind shrinkage and provide actionable, step-by-step tips, from fabric selection to post-production quality control. By implementing these strategies, you can minimize returns, build customer trust, and create a reputation for producing high-quality, long-lasting sweatshirts.
Why Sweatshirt Shrinkage Is a Major Issue for Manufacturers
Shrinkage isn’t just an inconvenience for the end-user; it’s a significant business problem for manufacturers. A sweatshirt that shrinks after the first wash can lead to a wave of customer complaints, negative reviews, and a high rate of returns. This not only erodes customer trust but also hits your bottom line through replacement costs, shipping fees, and damaged brand reputation.
In today’s e-commerce landscape, a single negative review about sizing issues can deter hundreds of potential buyers. For brands and businesses that order custom apparel, receiving a batch of sweatshirts that shrink and no longer fit their employees or customers is a disaster. It can disrupt marketing campaigns, uniform programs, and retail sales.
This is why mastering the process of **how to manufacture non-shrink sweatshirts** is a core competency for any reputable apparel producer. It’s about delivering on the promise of quality and ensuring the garment’s integrity from the factory to the consumer’s closet.
Understanding the Science of Fabric Shrinkage
To prevent shrinkage, you must first understand why it happens. Fabric shrinkage is a natural phenomenon, primarily occurring in natural fibers like cotton. During the manufacturing process, fibers are stretched and tension is applied during knitting, weaving, and finishing.
When the fabric is exposed to heat and moisture (in a washer or dryer), these fibers relax and return to a more natural, unstressed state. This relaxation causes the garment to contract, or shrink.
The type of fiber, the knit structure, and the finishing processes all play a critical role in the final shrinkage percentage. Cotton, which is a key component of most sweatshirts, is particularly susceptible to this process. Synthetic fibers like polyester are more stable and less prone to shrinkage, which is why blends are often used to mitigate the issue. Controlling these factors is key to **avoiding sweatshirt shrinkage**.
Step 1: The Role of Fabric Selection in Preventing Shrinkage
The journey to a non-shrinking sweatshirt begins with the fabric itself. Choosing the right material is the single most important decision a manufacturer can make. When sourcing fabric for custom sweatshirts, look for materials that have a stable knit structure. A dense, tightly knit fleece or French terry fabric will inherently be more stable than a loose-knit one.
For brands and manufacturers focused on quality, the type of fiber is crucial. While 100% cotton can be prone to shrinkage, a high-quality combed or ringspun cotton offers better stability. For the **best fabric to prevent sweatshirt shrinking**, a cotton-polyester blend is often the ideal choice.
The synthetic polyester fibers provide a stable framework that resists contraction, making the garment much more dimensionally stable after washing. A reputable supplier will offer a range of fabric compositions and weights, allowing you to choose a material that balances comfort, durability, and shrinkage control. Sourcing is a critical first step in **avoiding sweatshirt shrinkage** and building a reliable product.
Step 2: Pre-Shrinking Fabric During the Manufacturing Process
The most effective method for controlling shrinkage is to pre-shrink the fabric before cutting and sewing. This process, known as compacting or sanforizing, uses steam, heat, and pressure to force the fibers to contract at the mill. By doing this, the fabric’s tensions are released before it is ever sewn into a garment, significantly reducing or eliminating shrinkage in the consumer’s laundry.
When you offer **pre-shrunk custom sweatshirts**, you are giving your clients peace of mind. They know the size they purchase will be the size that comes out of the dryer. This is a non-negotiable step for any manufacturer aiming for a premium product. Ensuring your fabric supplier has a reliable pre-shrinking process is a key quality control measure. This process is an investment, but it is one that pays off in reduced returns and enhanced customer satisfaction. The difference in quality between a pre-shrunk garment and a non-pre-shrunk one is immediately noticeable after the first wash.
Step 3: Best Practices for Cutting and Sewing to Minimize Shrinkage
Even with pre-shrunk fabric, poor cutting and sewing practices can reintroduce tension that leads to shrinkage. Fabric lays on large rolls, and it’s essential to let it rest or “relax” before cutting. This allows any residual tension from the roll to dissipate. Cutting the fabric when it is still under tension can lead to uneven shrinkage and distorted garment shapes.
During the sewing process, it’s important to use the right needles and threads to avoid stretching the fabric. Using techniques like double-needle stitching and chain stitching can provide durability without compromising the fabric’s integrity. Ensuring seams are not pulled or stretched during assembly is critical. These best practices are fundamental to **anti-shrink sweatshirt production** and require skilled operators and vigilant supervision.
The Impact of Dyeing and Finishing on Fabric Stability
The dyeing and finishing processes also have a significant impact on a fabric’s dimensional stability. The high temperatures and water used in dyeing can cause significant fiber relaxation. It is crucial to monitor temperature and time during this phase to minimize shrinkage. Post-dyeing treatments, like tumbling or curing, can further help lock the fabric’s shape in place.
A high-quality finishing process, such as silicone washing or enzyme washing, can make the fabric softer, more stable, and resistant to future shrinkage. These treatments can also improve the fabric’s feel and overall quality. Partnering with a dye house that has experience in managing dimensional stability is a key aspect of **avoiding sweatshirt shrinkage** from a manufacturing perspective.
Quality Control Measures to Ensure Consistent Sizing
A rigorous quality control program is your final line of defense against shrinkage issues. This goes beyond a simple visual inspection. It should include pre-production testing and post-production audits. Before a production run begins, you should wash and dry a sample of the fabric to test its shrinkage rate.
This allows you to adjust your patterns to account for any expected shrinkage. After a batch of garments has been produced, random pieces should be pulled from the line and put through a wash and dry cycle. The dimensions should be measured against a standard to ensure they meet the acceptable shrinkage tolerance.
This process, known as **quality control for sweatshirt sizing**, is a crucial step in delivering a consistent and reliable product. At Divest Impex, every batch of fabric undergoes rigorous testing to ensure it meets our strict shrinkage standards, guaranteeing consistent sizing across all orders, from custom men’s sweatshirts to options for the whole family.
Educating Your Customers on Proper Garment Care
Even if you’ve done everything right in the manufacturing process, a consumer can still cause shrinkage through improper care. As a manufacturer, it is your responsibility to provide clear, easy-to-understand care instructions. The hang tag or sewn-in label should clearly state “wash cold, tumble dry low or hang dry.”
Explain why these instructions are important. Mention that high heat is the primary cause of fiber contraction. This small step can significantly reduce the number of customer complaints. Providing a guide on your website on “How to Care for Your Sweatshirt” can also build trust and show your brand’s expertise. Empowering your customers with knowledge is a proactive way of **avoiding sweatshirt shrinkage** post-purchase.
Investing in High-Quality Manufacturing Equipment
The right equipment can make a world of difference. Modern industrial dryers and tension-controlled spreading machines can help prevent stretching and minimize fiber stress during the production process. A manufacturer that invests in state-of-the-art machinery is better equipped to produce dimensionally stable garments.
For example, using a tunnel dryer with precise temperature controls can help set the fabric and prevent future shrinkage without causing damage. The investment in quality equipment is a sign of a manufacturer’s commitment to producing a superior product. This is a key factor in efficient **anti-shrink sweatshirt production**.
Comparing Cotton vs. Blended Fabrics for Shrinkage Control
When selecting fabrics, the choice between 100% cotton and a cotton/poly blend is a major consideration for manufacturers focused on **avoiding sweatshirt shrinkage**.
Here’s a quick breakdown:
- **100% Cotton:** Offers superior breathability and a soft, natural feel. However, without proper pre-shrinking, it can shrink significantly (up to 7-10%). It requires more care from the consumer.
- **Cotton/Polyester Blend:** Provides excellent dimensional stability due to the synthetic polyester fibers, which are resistant to shrinkage. It’s often more durable, wrinkle-resistant, and holds its shape better. A common blend is 80/20 or 50/50.
For manufacturers, a blend is often a safer choice for guaranteeing a consistent size. However, if you are committed to the feel of 100% cotton, a rigorous pre-shrinking process is absolutely essential to manage expectations and provide a high-quality product. This choice of material is fundamental to your overall shrinkage prevention strategy.
Case Study: A Manufacturer’s Success Story in Shrinkage Prevention
Let’s look at a real-world example. A large university clothing brand was facing a high rate of returns due to inconsistent sweatshirt sizing after washing. Their supplier was using a low-cost, non-pre-shrunk cotton fleece. The brand switched to a new partner, Divest Impex, which implemented a multi-step anti-shrink process.
This process included using a sanforized cotton/poly blend, precision cutting with relaxed fabric, and a final steam treatment. After launching their new line of **pre-shrunk custom sweatshirts**, the university brand saw a 90% reduction in returns related to sizing issues and a significant increase in positive customer reviews. This success story proves that investing in shrinkage prevention pays off in brand trust and customer satisfaction. It showcases the expertise of a manufacturer dedicated to solving this common problem.
Partnering with a Supplier That Prioritizes Shrinkage Control
For brands and businesses looking to source custom sweatshirts, choosing a manufacturer that has a proven track record in **avoiding sweatshirt shrinkage** is critical. You need a partner that is transparent about their fabrics, processes, and quality control measures. Ask them about their pre-shrinking methods, their QC procedures for sizing, and their fabric sourcing.
A reliable supplier should be able to provide data on their fabric’s shrinkage rate and offer a guarantee on sizing consistency. A manufacturer with a focus on quality will view shrinkage control as a point of pride, not a hidden cost. They will openly discuss their commitment to this process and how it benefits your brand.
Divest Impex is a premier manufacturer in Sialkot, Pakistan, known for its expertise in producing high-quality, pre-shrunk apparel. We serve clients globally, offering a wide range of custom sweatshirts, from custom women’s sweatshirts to custom kids’ sweatshirts, all manufactured with meticulous shrinkage control measures. You can trust our commitment to quality.
As of late June 2025, our manufacturing hub in Sialkot, Pakistan, is well-equipped to meet global demand for anti-shrink sweatshirt production. You can learn more about garment care from the Federal Trade Commission’s guide on clothing labels, which provides authoritative information for manufacturers and consumers.
FAQs: Your Questions About Sweatshirt Shrinkage Answered
- What is an acceptable shrinkage percentage for a sweatshirt?
- An industry-standard acceptable shrinkage rate for a well-made garment is typically between 3% and 5%. Any more than that is considered excessive and can lead to sizing issues. A manufacturer that offers **pre-shrunk custom sweatshirts** can often guarantee a rate of less than 3%.
- Does the washing temperature affect shrinkage?
- Yes, absolutely. Hot water causes fibers to relax more, leading to greater shrinkage. This is why care labels always recommend washing in cold water. Using a tumble dryer on a high heat setting is the single biggest cause of shrinkage after washing. To minimize shrinkage, always follow the care instructions provided by the manufacturer.
- Can I prevent shrinkage in a sweatshirt I already own?
- For consumers, the best way to prevent shrinkage is to wash the garment in cold water and air dry it or tumble dry on the lowest heat setting. Once a garment has shrunk, it is difficult to reverse the process without potentially damaging the fabric. The key is prevention through proper care. You can find more consumer-oriented tips from sources like Good Housekeeping.
- Is the thickness of the fabric related to shrinkage?
- Yes, to some extent. Heavier, denser fabrics are often more stable and less prone to shrinkage than lightweight, loosely knit fabrics. However, the pre-shrinking process is more important than the weight of the fabric. A properly pre-shrunk lightweight fabric will shrink less than a non-pre-shrunk heavyweight one.
- What is the best fabric for avoiding sweatshirt shrinkage?
- A high-quality cotton/polyester blend is often considered the **best fabric to prevent sweatshirt shrinking**. The polyester fibers provide a stable structure that resists the tension release that causes natural fibers to shrink. A pre-shrunk blend offers the best of both worlds: comfort and dimensional stability.
Newsletter
Subscribe my newsletter to get the latest posts delivered right to your email.